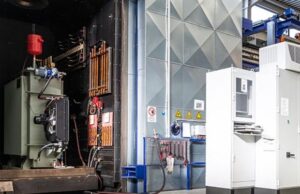
Even if the wind power industry is a growth sector now as before, the manufacturers are under fierce competition and cost pressure. The index of “Cost of energy“ is decisive, i. e. the ratio of operating expenses to energy yield.
This calculation includes the level of efficiency, availability and maintenance effort. This means for the manufacturers: efficiency, quality, and reliability of the machines have to comply with the highest standards. The drive train is essential here. This applies to all application fields of wind power plants (onshore, offshore, repowering, weak wind regions).
Another trend is the increasingly higher performance of plants specifically in the offshore field. Currently, plants having a power of 8 MW and rotor diameters of 170 meters are built.
For more than 25 years KTR has developed and manufactured drive components and systems for more than 100,000 wind power plants. The product portfolio comprises couplings with and without overload protection and torque measurement as well as rotor and yaw brakes.
Here, those projects are the main concern of the engineers of KTR’s business unit. “Engineered Business” requires cooperation and working closely with the design engineers of the plant manufacturers. The requirements include intensive testing on KTR’s in-house test field at the headquarters in Rheine and Schloß Holte-Stukenbrock as well as extensive product documentation and traceability of the different coupling and brake systems. KTR’s solution is called “KTR Ident.” The system collects all product-related data during the entire value-added process, prepares it in detail and issues it automatically, including all necessary documents such as certificates, test certificates, etc. KTR Ident identifies, documents and allows for traceability of product specifics, materials as well as manufacturing and assembly processes.
KTR
www.ktr.com/us/
Leave a Reply